航空整體葉輪五軸(zhóu)數控加工仿真及參數優化研究(上(shàng))
2016-11-21 來源:天津職業技術師範大學 作者:盧輝
摘要
航空整體葉輪(lún)的加工手段、加工精度和加工表(biǎo)麵質量直接影響葉輪的工作性能,對發動(dòng)機性能有決定性(xìng)的影響。作為一種典型的通道類複雜高精度零件,其葉片間流道間(jiān)距較小,葉片扭曲度大,其幾結構複雜(zá)對加工造成很大困難(nán),主要采用五軸數控機床進行(háng)加工(gōng)。雖然目前(qián)進行了針對航空整(zhěng)體葉輪較多的加(jiā)工仿真及(jí)參數優化研究工作,但仍存在如下問題:
(1)在參數優化研究方麵,未(wèi)考慮機床穩定性問(wèn)題(tí),在機床穩定的前提下開展加工參數優化研究,才能同時保證五軸(zhóu)加工的效(xiào)率和質量。
(2)由於葉片扭曲大(dà),通常CAM軟件生成的數控程序隻(zhī)考慮刀具(jù)與工件的幹涉,未考慮(lǜ)機床主軸(zhóu)與夾具、工(gōng)作台的碰撞,不能完全確保刀具(jù)軌(guǐ)跡的正確性和機床(chuáng)的安全性,因而需要(yào)考慮具體工藝係統,進行更全麵的幾何仿真研究。針對(duì)以上問(wèn)題,本文的主要研究工作(zuò)如下:
1.基於VERICUT的航空整體葉輪加工數控仿真建模。
在VERICUT 環境下建(jiàn)立虛擬的數控機床實體、控製係統、刀庫、坐(zuò)標係統等,創建數控仿真環境,實現針對具體工藝係統的幾(jǐ)何仿真(zhēn),有效避免機床主軸、刀具與工作台、夾具之間碰撞。
2.提出基於齊次變換的航空整體葉輪數控程序後處理(lǐ)算法。
首先針對海德漢i TNC530數控係統的傾斜加(jiā)工(gōng)麵功能,通過對CLSF刀位軌跡進行齊次變換運算,提出了機床運動坐標的數控程序後處理算法。使用(yòng)UG NX8.5/Post Builder編寫後處理文件,通過NC代碼(mǎ)分析、VERICUT仿(fǎng)真驗證後處理方法的正確性。
3.基於Cutpro9.0的工藝係統顫振穩定域獲取。
首先采用力傳(chuán)感器和(hé)加速度傳感器,通過(guò)錘擊實驗來獲取機床-刀具和機床-工件的(de)頻響函數。然後采用Cutpro9.0的動力學仿真功能,在給定的徑(jìng)向切削深度(dù)(切寬)條件下,進行顫振穩定域仿真,獲得表征主軸轉速和軸向切深關係穩(wěn)定域葉瓣圖。
4.基於幾何仿真和動力學仿真的切削參數優化。
在工(gōng)藝係統(tǒng)顫振穩定域仿真的基礎上,以切削時間為優化目標,切削深度、主軸轉速(sù)、每齒進給量為實(shí)驗因素,設計三因素四水平的正交試(shì)驗,通過幾何仿真獲得切削時間。根據極(jí)差分(fèn)析和方差(chà)分(fèn)析,得出三組較短切削時間的加工參數。對初步優化得到的三組切削參數進一步進行動力學仿真,根據仿真結果確定最優(yōu)工藝參數(shù)。
關鍵詞:航空整體(tǐ)葉(yè)輪,幾何仿真,動力學仿真,參數優化,正交試驗
第 1 章 緒論
1.1 課題研究背(bèi)景
航空整體葉輪是典型的通道類複雜零(líng)件(jiàn),其葉片間流道間距較小,葉片扭曲度(dù)大(dà),其幾何結構複(fù)雜對加工造成很大困難。加工方法、加工精度和加工表麵質量直接影響葉輪的工作性能,對發動機性(xìng)能有決(jué)定性的影響。航空整體葉輪因其曲麵的複雜性和加工精度高,使其成為典型的難加工零件[1-4]。
目(mù)前航空整(zhěng)體葉輪的加工一般采用數控多軸(zhóu)技術、電解技術、放電技術、鑄造技術等加工(gōng)方法。鑄造加工整體葉輪的特點是成本較低,適用於大(dà)批量的葉輪生產。這(zhè)種加(jiā)工方法的不足之處在(zài)於(yú)會產生內部結構缺陷,如砂眼、氣孔等(děng)。這可能導致葉片強度差,並最終影響成型零件的工作性(xìng)能(néng)。電火花和電解(jiě)加工可應用於各種難加工材料,加工穩定性高(gāo),零件質量較好。放電加工的缺點(diǎn)是加工(gōng)效率低,成(chéng)本高;而電解(jiě)加工效率較高,但精度較低。數控多軸技術可以加工多種類型的葉輪,加工精(jīng)度高,表麵光潔度好,因此航空整體葉輪加工常采用數控多軸技術(shù)[5]。
對於航空鋁整體葉輪來說(shuō),使用五軸機床進行高速切削(xuē)是最佳的加工方法。但當前航空(kōng)整體葉輪五軸加工(gōng)過程(chéng)仍存在很多工藝問題(tí),比如葉輪粗加工效率低,薄壁件加工易出現顫振導致葉片表麵光潔度差,切削參數選取不當導致刀(dāo)具折斷等。此外,到目前為止,切削參數的選擇尚未有一個完善的方法理論進行指導,實際生產加工中切削工藝參數往(wǎng)往取決於工藝人(rén)員的經驗。對於高速高精加工來說,尤其是葉輪具有複雜曲麵薄壁類零(líng)件,往(wǎng)往(wǎng)很難獲得(dé)預期的加工質量。其(qí)根本原因在於設定高速切削參數中沒有考慮機床的動力學特性,沒有考慮刀具振動對工件質量的影響,沒有考慮機床各軸的行程極限和加速度方麵的差異[6]。
1.2 課題的目的及意義
五軸加工航空整體葉輪過程中,刀軸(zhóu)變化頻繁易發生(shēng)碰撞,且葉片(piàn)厚度薄容易發生顫振,這些(xiē)因素製約著航(háng)空整體葉輪的高效高精加工。因此,本文通過建立VERICUT仿真環境檢查刀具軌跡(jì)避免機床與刀具(jù)發生碰撞,使用cutpro9.0軟件進行顫振穩定域分析和切削過程仿真,預測刀具(jù)振動、工(gōng)件振動、切削力、表麵粗糙度、主軸功率等,為合理地選擇加工參數避免發生顫振,能夠使五軸機(jī)床(chuáng)實現高速高精加工。本文研(yán)究內容有助於指導葉輪實際加工的切削參數的選擇,能夠為同類零件的加工提供(gòng)參考,具有重要的工程(chéng)應用價(jià)值。
1.3 國內外研究現狀
1.3.1 高速(sù)切削技術研究現狀
20 世紀 30 年代德國 Salomon 博士提(tí)出高速切削加工(HSM 或 HSC)概念,隨著切削速度(dù)提高到一定峰值(zhí)後(hòu),切削溫(wēn)度反而下降[7]。此後幾十年高速切削(xuē)加工的研究處於(yú)停滯狀態。從(cóng) 1950 年開(kāi)始世界各(gè)國(guó)開始對(duì)高速切削加工展開大規模研究,主要是歐美發達國家、蘇聯、澳大利亞、日本等國家[8-10]。這一時期稱(chēng)為高速切削理論研究的探索(suǒ)階段。到了 20 世(shì)紀(jì) 70 年代,高速切(qiē)削加工進入應用基(jī)礎研究(jiū)階段。1972 年到 1978 年美國洛克希德導彈與空(kōng)間公司研究小組主要研究(jiū)高速加工應用於生(shēng)產加工的可行性[11]。1980 年代高速切削加工研究開始進入應用研究階段。1979 年美國高級研究工程(chéng)局開始對高速切削工藝係統(tǒng)做全(quán)麵的研(yán)究,包(bāo)括高(gāo)速刀具、高(gāo)速機床、高速工藝等方麵[12]。1984 年至 1988 年德國研究技術部對高速切(qiē)削金屬和非金屬材(cái)料、高速(sù)切削(xuē)電主軸係統等研究,為(wéi)高(gāo)速(sù)切削技(jì)術應(yīng)用於實際加工打下(xià)結實的基礎[13]。進入 20 實際 90 年代後,隨著直線(xiàn)電機,機床電主軸、高速切削刀具的出現,高速切削加工機床不斷出現(xiàn)在國際市(shì)場,高(gāo)速(sù)切削加工進入到(dào)工業應用階段[14-17]。
相對於國(guó)外,國內對(duì)高速切削(xuē)研究起步比(bǐ)較晚,從 1980 年國內各大研究機(jī)構和(hé)大學開始對高速切削進行全麵研究。1980 年山東大學開始對高速切削中切削溫度、切削力、切屑、刀具壽命等(děng)研究[18]。20 世(shì)紀 90 年代後,北京理工大學研究了高速切削的刀具與切削力[19],廣東工業大學研究了高主軸轉速的電主軸技術、直線(xiàn)電動機進(jìn)給(gěi)係統[20],天津大學和大連理工大學從切削原理方麵入手研究高速切削(xuē)加工[21]。盡管國內的高(gāo)速切削技術與西方工業發達國家還有很大差距,但是經過國內大學的研究者努力和奮鬥,國內也出現了一(yī)批高速切削機(jī)床,如大連機床廠生產的高速加工中(zhōng)心。
高速切削與傳統加工相比具有(yǒu)以下優點,1)高速切削主軸轉速高,切削速度快,單位時間內去除材料(liào)體積增大,縮短切削時間,提高加工效率。2)高速切削時,切(qiē)削深度小,進給(gěi)速度快,故其切削力小。3)高(gāo)速切削時,切屑以很快地速度排除,帶走大部分的熱量(liàng),工件熱變形小。4)高速切削中隨(suí)著切削速度提高,切削力逐漸(jiàn)減小(xiǎo),而切削力是切削過程中振動(dòng)的主要來源,因而減(jiǎn)少切削振(zhèn)動,提高表(biǎo)麵粗糙度。5)高速切削可加工淬硬材料,減少電火花放電加工。正是由於高速切削具有以上特點,高(gāo)速(sù)切削技術(shù)廣泛應用於航(háng)空航天、汽車、模具等行業,尤其是在航空行業應用最多。航空製造中大部分是輕合金材料,且大(dà)都是薄壁類零件(jiàn),切削中容易變形(xíng)。高速切(qiē)削技術切削速度快,切削力小(xiǎo),特別適用(yòng)於航空類零(líng)件加工。
1.3.2 數控加工仿真技術研究現(xiàn)狀(zhuàng)
用於數控仿真(zhēn)和切削(xuē)參數優化方麵的(de)係統軟件主要有以下兩類:幾何仿真軟件和(hé)動力學仿真軟件(jiàn),幾(jǐ)何仿真是完成數控程(chéng)序(xù)的幾何仿真、進行刀具與機床、夾具的碰撞檢查以(yǐ)及(jí)對數控代碼的優化(huà)。目前,關(guān)於數控加工幾(jǐ)何仿真(zhēn)的研究已經(jīng)很(hěn)成熟了,並(bìng)且有很多幾何仿真軟件應用於實際生(shēng)產中。幾何仿真軟件最具代表性的軟件是(shì)CGTEC公司的VERICUT軟件[22]。VERICUT是交互仿真的NC程序數據去(qù)除材(cái)料過程。VERICUT軟件仿真(zhēn)可(kě)以替(tì)換昂貴的NC數據驗證過程,並且可以優化材料去除率。VERICUT通過仿真NC程序,可以減少或消除傳統費時費力的數控程序試切驗(yàn)證(zhèng)過程。到了90年代很多CAD/CAM集(jí)成軟件推出幾何仿真模塊,比如英(yīng)國的Power MILL,美國的Master CAM, 德國西門子公司的UG NX等軟件。這些CAD/CAM集成軟(ruǎn)件(jiàn)隻能進行前置代碼(mǎ)仿(fǎng)真,不能進行後置代碼仿真(zhēn)。在國內,1994年6月哈工大研發的三維動(dòng)態圖(tú)形仿真(zhēn)器NCMPS[23]。1994年11月由清華大學和華(huá)中科技大學合作研發的HMPS[24]。北京航空航天大學開發的集成在CAD/CAM係列軟件中的仿真(zhēn)模塊。
動力學仿(fǎng)真則須通過仿(fǎng)真切削過程中(zhōng)的主軸功率、切削力等預測加工精度和加工表麵質(zhì)量(liàng),為調整和優化切削參數提供依據,最終達到優(yōu)化結果。隨著計算機仿真技術的發展和對切削原理的研究越(yuè)來越深(shēn)入,目前以優化切削(xuē)參數為目的動力學仿真係統研(yán)究進展也很快。國外有加拿大UBC大學MAL實驗室[25]開發的Cutpro9.0、英國的Meltal Max,其(qí)中Cutpro9.0軟件可以利用虛擬現(xiàn)實和仿真(zhēn)技術對高速加工過(guò)程中的切削力、功(gōng)率、扭矩、切屑厚度、振動情(qíng)況(kuàng)等進行預測,以(yǐ)確定無顫振條件下的主軸轉速、進給量和切深,在保證良好表麵質(zhì)量的前提下提高材料的去除速率。這(zhè)些軟件已在包括波音、加普惠等數十加跨國公司得到了廣泛的(de)應用,並取得了(le)很好的效果。國內目前主要有北航自主開發(fā)的銑削加工(gōng)動力學仿真係統(tǒng)Simu Cut和數控機床動力學特性參數測試與分析Dyna Cut係統。該係統功能與Cutpro9.0基本類似,且已在國內軍工口幾十家(jiā)企(qǐ)業得到初步應用,不足之處是目前僅限於銑削加工仿真[26-27]。
1.3.3 切削顫振研究現狀
切削過程由於主軸的旋轉運動和刀具切(qiē)削工件產生的切(qiē)削力(lì)不可避免會出現振動情況。尤其是當切削參數選(xuǎn)取不當或切(qiē)削量過大時,刀具(jù)的振(zhèn)動會更加激烈。切削過程中產生的振動,會影響(xiǎng)加工質量和生產效(xiào)率,嚴(yán)重時甚至(zhì)會導致刀具斷裂,因此通常都(dōu)是對切削加工不利的(de)。切削振動主要表現在影響(xiǎng)加工的表(biǎo)麵光潔度、切削效率、刀具壽(shòu)命(mìng)、機床精度。多年來,國內外很多研究者對切削振動進行深入的研究,取得了可(kě)喜的成效。
在國外,Tobias[28]和(hé)Tlusy[29]通過對切削過程中的顫振現象的研究,提出了有關於主軸轉速和(hé)切削(xuē)深度的穩定臨(lín)界切削深度表(biǎo)達式,並對銑削穩定性進行了時域分析。Y.Altintas[30]通過(guò)切削過程(chéng)仿真建(jiàn)立動態銑(xǐ)削力的模型,提出(chū)了球頭銑刀進行穩(wěn)定切(qiē)削的方法,從而得到了切削深度與主軸轉速的顫振穩定分析解。該方法僅需要獲取整個工(gōng)藝係統的傳遞函數(FRF),切削力係數,徑向切深及統刀齒數,通(tōng)過較少量的計(jì)算得(dé)到較精確(què)的穩定性曲線。由於該方法對方向係數做傅裏葉變換後(hòu)僅取零次諧波分量,因此該方法被稱為零階求解方法(Zero Oder solution, ZOA)。Sata T等[31]在機床-刀具和機床-工件等動力學模態參數對切削穩定性影響分析的基礎上,給出了切削(xuē)速(sù)度、每齒進給量和刀(dāo)軸切削(xuē)角度的控製策略,得出了一種預測(cè)和控製顫振的(de)方法。Gagnol等[32]通過采用與速度無關的頻(pín)響函(hán)數(shù)來(lái)實(shí)現(xiàn)顫振穩定域預測,提(tí)出的顫振穩定域預測模型中考慮(lǜ)了主軸轉速對刀尖點(diǎn)頻(pín)響函數的影響。
在國內,師漢民等人(rén)[33-35]提出切削中發生顫振時,振幅大到一(yī)定(dìng)值之後趨於穩定,這是因為切削用量有限,當刀(dāo)具振幅比(bǐ)較大時刀具(jù)有一部分已(yǐ)經脫離工件不參與(yǔ)切削。機床顫振振幅(fú)穩(wěn)定模型主要受(shòu)到兩(liǎng)個非線性因素影響,第(dì)一刀具切削中脫離工(gōng)件不參與切削,第二切削(xuē)力的非線性特性(xìng)。熊(xióng)國良等[36]采用廣義(yì)傅裏葉級數法分析圓柱立(lì)銑刀的顫振問題,研究了主軸(zhóu)的陀螺效應(yīng)對工藝係統穩定性的(de)影響。石(shí)莉等[37]采用小波分析法對(duì)切削(xuē)力信號進行分析,根據切削力的波動來預測切削顫振,得到產(chǎn)生顫振的切削力(lì)信號(hào)範圍,從而給避免顫振提供一個參考。劉安民等(děng)[38]通過分析加工噪音來判斷是否發生顫振,從分析顫振噪音中得到(dào)顫振頻率,從而不需要測量(liàng)機床-工件和機床-刀具的傳遞函(hán)數,就可以建立動態切削力模型,得到主軸轉速和切削深度的穩定曲線。
1.3.4 切削參數優化研(yán)究現狀(zhuàng)
在國內,閆國琛[39]對S50C模具鋼高速(sù)切削加(jiā)工進行(háng)工藝(yì)參數優化研究,采用正交試驗得(dé)出模具鋼表麵粗糙度影響因素的規律(lǜ)情況,並基於(yú)BP 神經網絡和遺傳(chuán)算法進行工藝(yì)參數優(yōu)化。陳展翼[40]通過高速銑削試驗對鈦合金TC4材料進行正交試驗得到切(qiē)削參數對表麵粗糙度的影響規律,並利(lì)用遺傳優化算法實現(xiàn)了銑削加工參數優化。黃豪[41]基於不同切削方式(shì)的切削原理是(shì)相同的理論,針對不同的切削方式建立統一的(de)數(shù)學(xué)模型,在遺傳算法中加(jiā)入模擬退(tuì)火算法算子,提出(chū)混合遺傳算法並對其進行測試和驗(yàn)證(zhèng)。莊光法[42]對油管接箍內壁的車削加工中易發(fā)生變形超(chāo)差,加工效(xiào)率低(dī)下等問題,采用(yòng)Deform軟件和(hé)正交試驗進行切(qiē)削力預測得出切削因素對切削力影響的主次因素,並基於粒子群算法以最小圓度誤差和最大(dà)生產率為目標進行切削參數優化。
在國外,H. Kurtaran[43]通過(guò)耦合響應曲麵法(RSM)與開發的遺傳算法(GA)以最小表麵粗糙度為(wéi)優化(huà)目標進行切削參數的(de)優化。首先使用RSM建立表(biǎo)麵粗糙度值的數學模型,再通過遺傳算(suàn)法進一(yī)步優化切(qiē)削參數,最終得到最佳切(qiē)削參數。Franci Cus[44]基(jī)於神(shén)經網(wǎng)絡對切削參數進行多目標進行優化,通過充分考(kǎo)慮技(jì)術、經濟等(děng)因素多目標優化(huà)。為了達到更精(jīng)確的預(yù)測結(jié)果,該神經網絡優化算法能夠實現對重要的切削參數簡單、快速(sù)和高效的優化。該方法適用於快速確定最佳切削參數(shù)的加工。Petropoulos[45]等提出使用幾何規劃方法進行數控車切削參數優化,該優化方法綜(zōng)合(hé)考慮機床的最大主(zhǔ)軸功率和(hé)切削速度等因素,以最小生產成本為優化目標。但(dàn)該模型(xíng)約束條件多,計算量(liàng)大,效率低下。Eskicioglu和Jha考慮了這個問題[46],提出了基於幾何規(guī)劃法和拉格朗日乘(chéng)數法的算法,以減少約束數目,減少運算量。1.4 本文主要研究內容 航空整體葉輪的加工(gōng)手(shǒu)段、加工精度和加工表麵質(zhì)量直接影響(xiǎng)葉(yè)輪的工作性能,對發動機性(xìng)能有決定性的影響。作為一種典型的(de)通(tōng)道類複雜(zá)高精度零件,其葉(yè)片間流道間距較(jiào)小,葉片扭曲度大,其幾何結構複雜(zá)對加工造成很大困(kùn)難,主要采用五軸數控(kòng)機床進行(háng)加工。雖然目前進行了針對航空整體葉輪較多的加工仿真及參(cān)數優化研究工作,但仍存在(zài)如下問題:(1)在參數優化研究方麵,未考慮機床穩定性(xìng)問題,在機床穩定的前提下開展加工參數優(yōu)化研究(jiū),才能同時保證五軸加工的效率和質量。(2)由(yóu)於葉片扭(niǔ)曲大,通常CAM軟件生成的數控程(chéng)序隻考慮刀具(jù)與工件的幹涉,未(wèi)考慮機床主軸與夾具、工作台的碰撞,不能完全確保刀具軌(guǐ)跡的正確性和機床的安全性,因而(ér)需要考慮具體工藝係統,進行更全麵(miàn)的幾(jǐ)何仿真研究。針對以上問題,本文的主(zhǔ)要研究工作如下:
1.基於VERICUT的航空整體葉輪加工數控仿真建模。在(zài) VERICUT 環境下建立虛擬的數控機床實體、控製係統、刀庫、坐標係統等,創建數控仿真環境,實現針對具體工(gōng)藝係統的幾何(hé)仿真(zhēn),有效避(bì)免機床主軸、刀具與工(gōng)作台、夾具之間碰撞。
2.提出基於(yú)齊次變換的(de)航空整體葉輪數控程序後處理算法。首先(xiān)針對海德漢(hàn)i TNC530數(shù)控係統(tǒng)的傾斜加工麵功能,通過對CLSF刀位軌跡進行齊次變(biàn)換運算,提出了機(jī)床運動(dòng)坐標的數控程序後處理算(suàn)法。使用UG NX8.5/Post Builder編寫後處理文(wén)件,通(tōng)過NC代碼分析、VERICUT仿真驗證後處理方法的正確性。
3.基(jī)於Cutpro9.0的(de)工藝係統顫振穩定域(yù)獲取。首先采用力傳感器和加速度傳感器,通過錘擊實驗(yàn)來獲取機床-刀具和機床(chuáng)-工件的頻響函數。然後采用Cutpro9.0的動力學仿真功能,在給定的徑向切削深度(切寬)條件下,進行顫振穩定域仿真,獲得表征(zhēng)主軸轉速和軸向(xiàng)切深關係穩定域葉瓣圖。
4.基於幾(jǐ)何(hé)仿真和動力學仿真的切削參數優化。在工藝係統顫振穩定域仿真的基礎上,以切削時間為優化目(mù)標,切削深度、主軸轉速、每齒進給(gěi)量為實(shí)驗因(yīn)素(sù),設計(jì)三因素四水(shuǐ)平的正交試驗,通過幾何仿真獲得切削時間。根據極差分析和方差分析,得出三組較短切削時間的加(jiā)工參數。對初(chū)步優化得到的三組切削參數進一(yī)步(bù)進行動力學仿真,根據(jù)仿真結果確定最優工藝參數。
第 2 章 葉輪五軸數控(kòng)加工幾何仿真
2.1 概述
由於航空整體葉輪五軸加(jiā)工過程中刀(dāo)軸變化頻繁,容易產生刀具幹涉或過切現象。隨著主軸的擺動(dòng)或(huò)工作台的旋轉,如果考慮不(bú)周全,主軸與工作(zuò)台或主(zhǔ)軸與夾具之間極易發生碰撞。為了解決這一問題,本節在VERICUT 環境下建立虛擬的數控機床實體、控製係統、刀庫、坐標係統等,創建數控仿真環境,實現針對具體工藝係統的幾何仿真,有效避免機床主軸、刀具與工作台、夾具之間碰撞考慮機(jī)床(chuáng)刀具與夾具、工件(jiàn)之間的碰(pèng)撞,檢查過切現象(xiàng)。
2.2 VERICUT軟件簡介
2.2.1 VERICUT簡介(jiè)
美國CGTEC公司的VERICUT軟(ruǎn)件是最具代表性(xìng)的幾何仿(fǎng)真軟件。其(qí)主要功能是完成數控(kòng)程序的幾(jǐ)何仿真、進行刀具與(yǔ)機床、夾具的碰撞檢查以及對數控代碼的優化。VERICUT可以與世界上(shàng)主流的CAM軟件進(jìn)行對接,主要解決模型轉換、NC程序傳輸等問題,提高加工過(guò)程仿真的效率。隨(suí)著數控(kòng)技術在實際生產應用(yòng)越來(lái)越多(duō),VERICUT軟件也得到了廣泛(fàn)應用。目前,國(guó)外很多大的航(háng)空公司汽車公司比如加拿大的龐巴迪公司、德(dé)國的大眾汽車公司、美(měi)國的波音公司等都(dōu)已經把VERICUT軟件應用(yòng)到生產實踐中,在國內使用VERICUT的公司有青島海爾股份有限公司(sī)、天津汽車模具股份有限公司、沈(shěn)陽飛機製造公司(sī)[47]。
VERICUT是交互仿真的NC程序數據去除材料過程。VERICUT軟(ruǎn)件仿真可以替(tì)換昂貴的NC數據驗證過程,並且可以優化材料(liào)去除率。VERICUT通過仿真NC程(chéng)序,可以減少或消除傳(chuán)統費時費力的數控程序試切驗證(zhèng)過程。它還可以優化(huà)程序中(zhōng)進給速度和主(zhǔ)軸(zhóu)轉速提高加工效率(lǜ)。這些能夠為企業以較低的成本(běn)進行生產,創造(zào)更(gèng)高的利潤。VERICUT能夠核實NC程序的準確性,能夠確保加(jiā)工完成的產品(pǐn)與設(shè)計的產品相匹配[48]。
2.2.2 VERICUT係(xì)統功能模塊
1.驗證與仿真模塊(kuài)
VERICUT模擬仿真可以進行5軸銑削,鑽孔(kǒng)和線切割,以及車(chē)銑複合等仿(fǎng)真。類似加工零件的要求,VERICUT仿真也需要NC程序數(shù)據,毛坯模型,以及加工中所需的刀(dāo)具模(mó)型。VERICUT幾乎可以仿真任何格式的數控程序,比如G、M代碼(mǎ)數據以及APT文件。驗證處理的(de)結果是加工完成的實(shí)體模型(xíng)和錯誤信息報告(gào)的日誌文件。仿真(zhēn)結果得到實體模型可(kě)以進行檢測,查看零件的過切或欠切情況,還可以保存(cún)用作另一個NC程序的毛坯模型。日誌文件記錄著在模擬過程中任何加工誤差和錯誤。VERICUT驗證模(mó)塊可以簡化傳統的試切驗證過程,減少產品的生產周期,提高生產率。
2. 數控程序優化
VERICUT優化模塊有自動和(hé)用戶自動義兩種方式,可以最大限度地提高材料去(qù)除率。VERICUT有恒定體積去除率和恒定切削厚度這兩種優化方法。恒定體積去(qù)除率的原理是通(tōng)過設定一個切削體積(Vol)來調節進給速度,

,其中ap為(wéi)切削深度,ae為切削寬度,F為進給速度。當切(qiē)削體(tǐ)積為零時(shí),說明機床正在空走(zǒu)刀,沒有切削工件,這樣可以適當提高切削速度;當切削體積大於優化庫中設定的值時,適當減少切削速度;當(dāng)切削體積小於(yú)優化庫中的值時,增加切削速度。恒定切削厚度的優化原理為通過變化進(jìn)給速度來保持恒定的切削厚度,這種(zhǒng)方法主要用於精(jīng)加工。
2.2.3 VERICUT機床加工仿真過程
要在 VERICUT 中實現加工仿真,首先需要建立(lì)虛擬機床,選擇(zé)控製係統,建立加工中所需的毛坯和加工刀具,然後輸入 NC 數控程序,設置(zhì)工件坐(zuò)標(biāo)係,開始仿真。仿真結束後,對仿真結果進行分析。仿(fǎng)真操作流程如圖 2-1 所示。
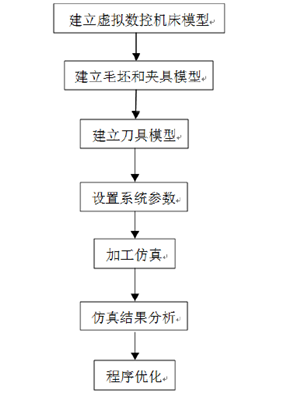
圖 2-1仿真操作流程圖
1.建立虛擬數控機床模型
VERICUT軟件中(zhōng)機床模型庫(kù)中有許多常見的機床模型,包(bāo)括了數控車床(chuáng),三(sān)軸加工(gōng)中心,五軸機床,電火花機床等。如果機床模型(xíng)庫中,沒有所(suǒ)需的機床模型。可以通(tōng)過三維建(jiàn)模(mó)軟件(jiàn)或VERICUT軟件進行建立機床模(mó)型,再通過VERICUT定義其機(jī)床的運動關係,這樣就可以建立自己所需的(de)機床。
2.建立毛坯和夾具模型
通過測量實際毛坯和夾具建立三維(wéi)模型,導(dǎo)入到VERICUT軟件中。建立夾(jiá)具模型主要是檢(jiǎn)查機床刀具或主軸與夾具的碰撞情況。毛坯模型是VERICUT軟件進行加工仿真的必(bì)備條件。
3.建立刀具模型
VERICUT仿真與實際加工一樣也是需要刀具的。VERICUT軟件中有建立刀具和刀柄的專用(yòng)模塊。
4.設置係統參數
在進行切削仿真之前,還需要設置一些係統參數,如(rú)工件坐標係,刀具換刀位置等。
5.加工仿真
建立完機床模型、夾具模型、刀具模型等,就可以(yǐ)導入NC數控程序進行加工仿真。
6.仿(fǎng)真結果分析
對於仿真結果,可以通過自動對比分析毛坯模型與設計模(mó)型的(de)差值,從而得到過切與欠切的情況。還可以通過(guò)查看仿真(zhēn)日誌文件,檢查切削(xuē)過程中機床與工件之間(jiān)發生的碰撞情況。通過分析仿真結果對數控(kòng)程序或裝夾方(fāng)案進行修改,以達(dá)到(dào)無(wú)錯誤(wù)的仿真結果。
7.程序優化
通過分析仿真結果,得(dé)到無碰撞無(wú)過(guò)切(qiē)的數控程序後,使用VERICUT優化(huà)模塊進行切削速度的優(yōu)化(huà),提高加工效率。VERICUT優化不會改變數控程(chéng)序原有的刀(dāo)具軌跡,隻(zhī)會改變進給速度和主軸轉速。
2.3 建立(lì)VERICUT虛擬數控仿真環境
2.3.1 VERICUT虛擬(nǐ)機床的建立
VERICUT虛擬機床的建立過程就是(shì)對實(shí)際機床(chuáng)進行測量在(zài)三維軟件中建立機床各部(bù)件的模型,導入到VERICUT軟件中按照實際運動邏(luó)輯關係進行“裝配”。VERICUT構建機床流程:第一建立機床各部件間運動關(guān)係;第二建立機(jī)床組件模型;第三設定機床(chuáng)相關參數。
本文選用的是DMG公司的HSC75 linear五軸高速加工中心,控(kòng)製係統(tǒng)是海德漢i TNC530。該五軸機床屬於刀具擺動與工作台回轉類型,如圖2-2所示。其(qí)機(jī)床主要參數如表2-1 所示。
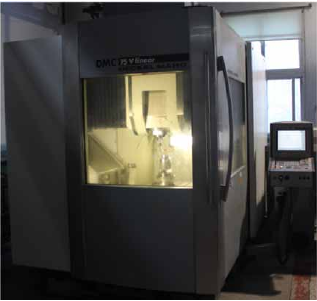
圖 2-2 德瑪吉 HSC75 機床
表 2-1 德(dé)瑪吉 HSC75 機(jī)床(chuáng)主要參數
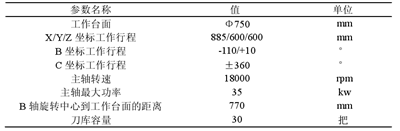
建(jiàn)立虛擬機床模型必須(xū)要了解機床各部件間的運動關(guān)係以及它們的依附關(guān)係,再將機床進行(háng)運動分解。通過分析機(jī)床的結構(gòu)可(kě)知HSC75有兩大運動鏈,主軸運動鏈(liàn)和毛坯運動鏈。主軸運(yùn)動鏈:Y軸依(yī)附於Base(床身),Y軸運(yùn)動不影響Base的狀態和位置變化;Z軸依附於Y軸,並會隨(suí)著Y軸(zhóu)的移動而改變位置;B軸依附於(yú)Z軸,並會隨(suí)著Z軸的移動而改變位置;主軸依附於B軸,並會隨著B軸的移動而改變(biàn)位置;刀具依附於主軸,並會隨著主(zhǔ)軸的移動而改(gǎi)變位置。即(jí)Base→Y→Z→B→Spindle→Tool。毛坯運動鏈:X軸依附於Base,X軸運動(dòng)不影響Base的狀態和位置變化;C軸(zhóu)依附於(yú)X軸,並會隨著X軸的移動而改變位置;夾具依附於C軸,並會隨著C軸的移動(dòng)而改變位(wèi)置;毛坯依附於夾具,並會隨著夾具的移動而改變位置。即Base→X→C→Fixture→Stock。建立的機床組件樹如圖2-3所(suǒ)示。
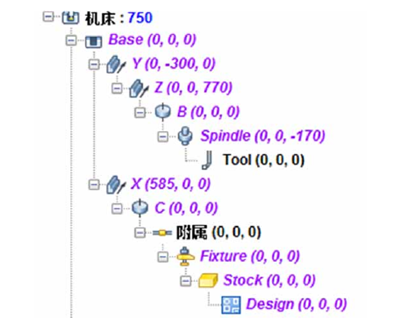
圖 2-3 HSC75 機床組件樹
建立完(wán)機床組件樹後,下麵就需要添加機床各部件的3D模型(xíng)。為了建模方便,本文將在UG軟件中建立機床各部件的三維模型,然後導出STL格式的機床模型文件,添加到VERICUT中。在UG中建立機床模型的(de)坐標係要和VERICUT中的(de)機床坐標係一致,建立(lì)各個軸的(de)模型時,須按照機床(chuáng)位於零點位置時各坐標軸的位(wèi)置及狀態來建模,這樣能有(yǒu)效減少後(hòu)續機床調試難度(dù)和時間。由於HSC75五軸機床的(de)B軸旋轉是機床主軸擺動,因此機床主軸在擺動過程中很容易與工作台、夾具等發生碰撞。這就(jiù)要求機床各運動軸的位置關係一定要與實際位置相一致。而其他機(jī)床部件比如機床麵板、機床外殼等可以(yǐ)進行簡化(huà)建模或者不需要建模,這樣可以減輕工作量(liàng)提高VERICUT仿真速度。 導入機床(chuáng)部件模型文件後,還需要進(jìn)行機床參數的設定,如機床機械原點、機床換刀位置、機床各軸行程(chéng)範圍等。打(dǎ)開“配置”——“機(jī)床設定”,按順序進(jìn)行設定碰撞檢測、表、行程極限、軸(zhóu)優先、子程序、機床(chuáng)備忘錄等參數。通過以(yǐ)上(shàng)設置,就(jiù)完成HSC75機床仿真模型建立(lì)如圖2-4所示。
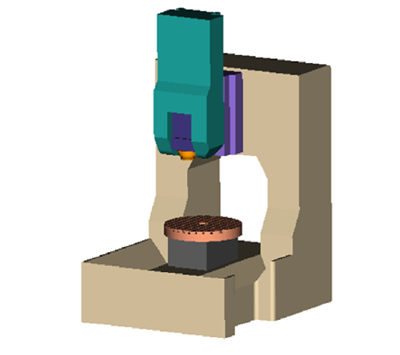
圖 2-4 HSC75 機床(chuáng)仿真模型
2.3.2 VERICUT虛擬刀具庫的建(jiàn)立
VERICUT軟件(jiàn)中有專用於建立刀(dāo)具和刀柄的(de)模塊(kuài),可(kě)以建立與生產加工一致的刀具和刀柄文(wén)件,如可以建立立銑刀、球頭銑刀、盤銑刀(dāo)、鑽頭等。選擇“項目”→“刀具(jù)”命令,係統彈出圖2-5所示(shì)的“刀具管理器”對話框。該對話框主要有4部(bù)分顯示區域:刀具號(hào)、刀具(jù)參數區、圖形顯示區和信息提示區,每個不同的區域可相互作用。
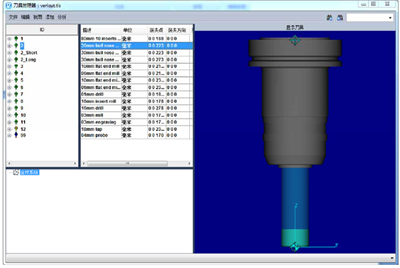
圖 2-5 刀具管理器對話框
在VERICUT係統中的“刀具管理”對話框中,用戶可以根據(jù)具體應用場合定義不同的刀具類型,包括銑刀、車刀、鏜刀、探(tàn)針、線切割刀具共5種類型。本文(wén)研究用到的刀具都是銑刀,按形狀可分為平(píng)底銑(xǐ)刀、麵銑刀、球頭銑刀、牛(niú)鼻銑刀和鑽削銑刀。
在圖2-5所(suǒ)示的“刀具管理器”對話框中選擇“添加”→“新”→“銑削”命令,係統將彈出圖2-6所示的對話框。在“組件類(lèi)型”下拉列表框中選擇不同的選項,對話框(kuàng)中需設置的內(nèi)容也不一樣。當“組件類型”下(xià)拉列表(biǎo)框中選擇“旋轉型刀具”時,可創建(jiàn)平頭銑(xǐ)刀或球頭銑刀等,按要求輸入刀具切削刃(rèn)結構尺寸即可(kě)。通過這種方法(fǎ),創(chuàng)建本文研究所需(xū)的刀具。
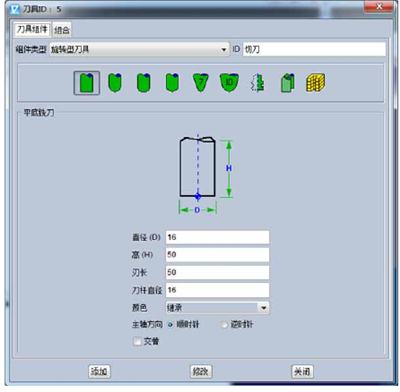
圖 2-6 旋轉型刀具對話框
2.3.3 VERICUT其他(tā)參數的設定
建立完機床和刀具庫後,需要設定(dìng)數控程序加工基(jī)準,也就是(shì)實際加工中所說的對刀。VERICUT提供的對刀方式有“基於工作偏置”、“機床零點(diǎn)”、“工作偏置(zhì)”、“程序零點”、“輸入程序(xù)零點”、“RTCP旋轉點偏置”及“RPCP旋轉點偏置”。本文使用程序零點對刀,打開G代碼偏置對話框如圖(tú)2-7所示。一般情況下主軸上不帶旋轉軸的機床對刀時,選擇Spindle組件,如果主軸上有旋轉軸,選擇主軸上的旋轉軸來對刀,主軸上有兩個或兩個以上的旋轉軸,選擇主(zhǔ)軸分支上線性軸下連續的旋(xuán)轉軸對(duì)刀(dāo)。
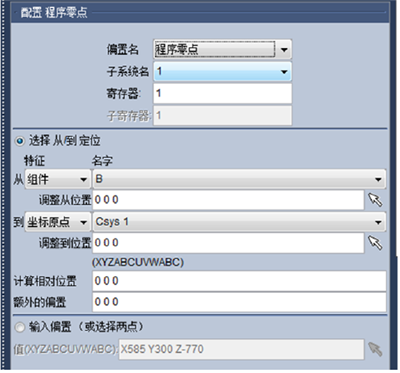
圖 2-7 G 代碼偏(piān)置對話框
2.3.4 VERICUT虛擬仿真(zhēn)環境驗證
構建好了機床模型後,下麵添加已經實際驗證過無碰撞的數(shù)控程序來進(jìn)行數控加工仿真,驗證HSC75虛擬機床的正確(què)性。操作步驟如下:
(1)右擊項目樹中“控製”→“打開”→“hei530.ctl”,加載hei530.ctl控製(zhì)文件。
(2)在(zài)組件模型樹中添加已經創建好的夾具和毛坯模型文件。
(3)設置加工坐標係(xì),右(yòu)擊“坐標係統”→“添加(jiā)新的坐標係”,創建一個Csys 1的坐標係,然後將坐標係移動到毛坯上表麵的中心,使Csys 1與編程加工坐標係重合。
(4)設置G—代(dài)碼偏置,在偏置名中選擇“程序零點”,子係統名為(wéi)“1”,點擊(jī)添加。選擇“從”特征為“組件(jiàn)”,名字為“B”,選擇“到”特征為“組件”,名字為“Csys 1”。
(5)加載之前所創建的(de)刀具庫
(6)添加數控程序
(7)在VERICUT主窗口中(zhōng),點擊右下角的“重置模型”按鈕,再點擊“仿真到末端”,開始數控加工過程仿真,仿真結果和自動-比(bǐ)較報告如(rú)圖2-8所示。
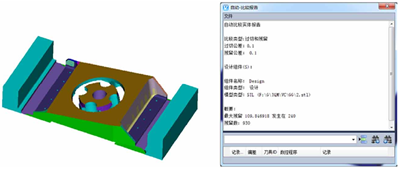
圖 2-8 仿真結果和(hé)自動-比較(jiào)報告
仿真結果圖沒有(yǒu)顯示紅色區域(yù),說明(míng)刀具沒有與夾具(jù)、工作台等發生碰撞;自動—比較分析報告(gào)隻顯示最大殘留部分,無過切信息,說明工件無過切現象。這就驗證了數(shù)控仿真環境 HSC75 虛擬機床的正確(què)性(xìng)。
2.4 本章小(xiǎo)結
本章節中,在 VERICUT 建立虛擬的數控機床實體、控製係統、刀庫、坐標係統等,創建一個數控仿真環(huán)境,檢驗機床各部件之間、刀具與夾(jiá)具之間及刀具與毛坯之間的(de)幹涉和碰撞,為(wéi)後續檢查葉輪加工幹涉做準備。同時,總結出幾點(diǎn)利(lì)用VERICUT軟件(jiàn)進行虛擬數控機床建模的關鍵技術。第一,根據實際數控機床各個運動坐標(biāo)軸和主要部件的運動邏輯關係來建立正確的機床運動組件拓撲關係;第二,在UG中創建機床三(sān)維模(mó)型,需要注意建模(mó)坐標係與VERICUT中的機床坐標係相重合,方便後續裝配機床;第三,設置G—代碼(mǎ)偏置時需要考慮機(jī)床的(de)結構,不同的機床結構對應不同的G—代碼偏置(zhì)。
投稿箱:
如果您有機床行業、企業相關新聞稿(gǎo)件發表,或進行(háng)資訊合作,歡迎聯係本網編輯部, 郵箱:skjcsc@vip.sina.com
如果您有機床行業、企業相關新聞稿(gǎo)件發表,或進行(háng)資訊合作,歡迎聯係本網編輯部, 郵箱:skjcsc@vip.sina.com
更多(duō)本專題新聞
專題點擊前十(shí)
| 更多(duō)