加工中心主軸箱體製造工藝可靠性保障方法的研究 (中(zhōng))
2017-6-30 來源:吉林(lín)大學(xué) 作者: 譚壯
第 3 章基於模糊評判的加工中心(xīn)主軸箱體製造工藝(yì)
FMECA 工藝 FMECA 方法能夠對加工中心(xīn)主軸箱體製造工藝中各個工序的工藝故障模式進行分析,尋找引發工藝故障模式的(de)原因,並針對各個工藝故障模式進行(háng)風險優(yōu)先數(shù)評分,對風險優先數不符合(hé)規定要求的加工中(zhōng)心主軸(zhóu)箱體製(zhì)造工藝故障模式製定改進措施,跟蹤(zōng)改(gǎi)進措施的有(yǒu)效性直到其風險優先數降低到(dào)符合規定要求為止,達到保障加工中心主軸箱體(tǐ)製造工藝可靠性(xìng)的目的。當缺少加工中心主軸(zhóu)箱體生產過程中相關統計數據時,將無法客觀計(jì)算出工藝故障模(mó)式的風險優先(xiān)數,進而無(wú)法判別出風(fēng)險優先數不(bú)符規定要求的工藝故障(zhàng)模式。為了(le)解決上述問題,本章采用梯形模糊評判的方法對不同原(yuán)因引起的(de)工藝故障模式進行排序,並對加工中心主軸箱體整個工藝流程進行綜合評判,為是否對整個工藝流程實施改進措施提供參考。通(tōng)過實(shí)例分析,驗證了該(gāi)方法的可行性。
3.1 加(jiā)工中心主軸箱體製造工藝 FMECA
FMECA 是故障(zhàng)模(mó)式、影響及危害性分析(Failure Mode,Effects and Criticality Analysis)的(de)簡稱,是(shì)用於歸納分析(xī)係統單元產生的故障(zhàng)模式、故障模式發生概率、嚴重程度及其影響後(hòu)果的一(yī)種(zhǒng)方法[68]。FMECA 由故障模式及影響(xiǎng)分析(Failure Mode and Effects Analysis,FMEA)和危害性分析(Criticality Analysis,CA)兩部分內容組成。上世紀五十年(nián)代初,美國一家飛機公司在產品研發(fā)階段首先采用了 FMECA 方法,隨(suí)著相關標準的製定,FMECA 方法在美國的航空航天以及(jí)船舶等領域得到了廣泛的應用。上世紀八十年代,我國將 FMECA 理論引進了國內,經過研究與學習(xí)後,製(zhì)定了一係列的標準並將其應用到了(le)多個行業領域。 根(gēn)據 FMECA 分析的對象不同可(kě)以分為功能 FMECA、硬件 FMECA、軟件FMECA、過(guò)程 FMECA 等。通過工藝 FMECA 對加工中心主軸箱體製造過程中每道工序所(suǒ)有可能發生的故障模式、故障(zhàng)原因、故障模式產生的影響、發生概率(lǜ)以及被(bèi)檢測難度進行分析,根據風險優先數評分確定出薄弱工序並製定改進措施,對改進措施執行後的故障(zhàng)模式風險優先(xiān)數進行預測或者跟蹤,使各個工序的所有(yǒu)工藝故障模式風險優先數滿足(zú)規定要求,從(cóng)而達到保障加工(gōng)中心主軸箱體製造工藝可靠性的目的。 根據(jù)國家軍用標準的要求[69],加(jiā)工(gōng)中心(xīn)主軸箱(xiāng)體製造(zào)工藝 FMECA 的分析步驟如下:
(1)對待分析的加工(gōng)中心主軸箱體特點、功能及相關要求等進行分析; 繪製“工藝流程(chéng)表”(用於分析加工中心主軸箱體每道工序的功能(néng)和要求)及(jí)“零部件-工藝(yì)關係(xì)矩陣”(對加工中心主軸箱體工(gōng)序(xù)按各(gè)個特性進行分類),上述兩個表格是工藝 FMECA 的前期準備工作;
(2)分析加工中心主軸箱體各個製造工序的工藝故障(zhàng)模式,常(cháng)見的工藝故障模式有:尺寸超差、形狀超差(chà)、變形、斷裂等;
(3)對工藝故障原因進行分析,常見的工藝故(gù)障原因有:刀具磨損、夾具磨損、熱處理時間不當等;
(4)對工藝故障影響進行(háng)分析,工藝(yì)故障(zhàng)影(yǐng)響包括對下道工序或(huò)者後續工序的(de)影響、對(duì)部件或者整(zhěng)機的影響(xiǎng),常見的工藝故障影響(xiǎng)有:無法加工表麵,部件不合格、整機可靠性低等;
(5)對風險優先數( RPN )進行分析(xī), RPN 值越大表明該工藝故障模式風險性越大,該工序越薄弱,RPN ?S ?O?D,其中 S 表示工藝故障模式的嚴酷度等級,O 表示工藝故障模式的發生概率等級,D 表(biǎo)示工藝故障模式的被檢測難度等級;
(6)對於風險優先數或者 S 、 O 、 D 指標(biāo)不符合規定要求的工(gōng)序製定有效改進措施,降低 S 、O 、 D 指(zhǐ)標(biāo)和風險優先數 RPN ;
(7)預測或跟蹤改進措施,直到風險(xiǎn)優先(xiān)數 RPN 滿足規定要求為止; 將分析結果歸納整理(lǐ),生成工藝過程 FMECA 報告,其主要內容包(bāo)括:加工中心主軸箱體特征概述、工藝(yì) FMECA 表格、結論及建議、相應的附表(如(rú)“工藝流程表”、“零(líng)部件-工(gōng)藝關係(xì)矩陣”)等。 圖 3.1 為加工中心主軸(zhóu)箱體製造工藝 FMECA 分析步驟(zhòu)的流程圖(tú)。
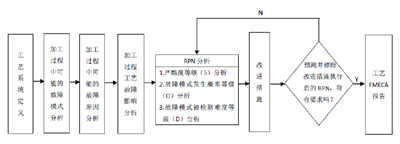
圖 3.1 加工中心主軸箱體製造工藝 FMECA 步驟
風險優先數( RPN )中的S 、O 、D 指標可參照國家軍(jun1)用標準[69]的評分要(yào)求進(jìn)行打(dǎ)分,但是需要生產過程(chéng)中的統計(jì)數據作(zuò)為評分參考。當生(shēng)產統計數據充足的時候,可以直接按照(zhào)國(guó)家軍用標準[69]對加工中心主軸箱體應用製造工藝FMECA 方(fāng)法(fǎ),對風險優先數不合規定(dìng)要求的工藝故障(zhàng)進行改進並跟蹤,直到(dào)其風險優先數降(jiàng)低到符合規定要求(qiú)為止,達到保障製造工藝可靠性的目的。由於企業對製造工藝可靠性的重視程度(dù)不夠或者某些型(xíng)號加工中心主軸箱體屬於小批量生產類型等原因,在執行風(fēng)險優先數( RPN )中的 S 、O 、D 指標評分時會出現生(shēng)產過程統計數據不(bú)足的情況,從而無法判別哪些工藝故障模式風險優先數(shù)不符合規定要求。為了解(jiě)決數據不足(zú)的問題,本文提出梯形模糊數評判與工藝FMECA 相(xiàng)結合的方(fāng)法。
3.2 梯形模(mó)糊數評判方法
3.2.1 相對風險程度梯(tī)形模糊數評(píng)判方法
相對風險程度(dù)梯形模糊數評判方法是將專家組對加工中心主軸箱體各個工藝(yì)故障模式的定性比較(jiào)轉化為定量計算的一種方法。梯形模糊數評(píng)判是一個(gè)向量(liàng),而不是單一的具體數值點,因此具有(yǒu)較高的判(pàn)斷準確性。本文(wén)定義梯形模糊數為M ,其隸屬函數 μ(x) : R-[0,1] 如下[70-71]:
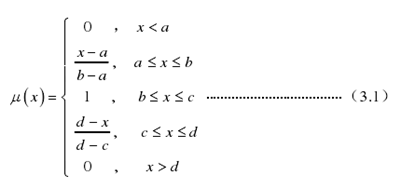
式 3.1 中a<b<c<d a 表示梯形模糊數 M 的上界,d 表示梯形模糊數 M 的下界,閉區間[b,c]表示梯形模糊數 M 的中值,當b ?c 時,梯形(xíng)模糊數 M 也被(bèi)稱(chēng)為三角形模糊數,(d? a)的值越大表示(shì)梯(tī)形模糊數 M 的(de)模(mó)糊程度越強,通常用 M?(a,b,c,d) 表示梯形模糊數。 本文邀請了一組加工中心主(zhǔ)軸箱體生產領域(yù)的專家,專家(jiā)組應由工藝設計人員,質保人員、車間檢測人員等組(zǔ)成。以風險優先數( RPN )為指(zhǐ)標對加工中心(xīn)主軸(zhóu)箱(xiāng)體製造工(gōng)藝過程中所有(yǒu)可能發(fā)生的工藝故障模式進行(háng)評價,專家組進行評價時需采用本文規(guī)定的以下語義(yì)詞:“沒有風險(xiǎn)”、“很小風險”、“較小(xiǎo)風(fēng)險”、“一般風險”、“較(jiào)大風險”、“很大風險”。梯形模糊數 M?(a,b,c,d) 可以對上述語義詞進行定量表示,為便於(yú)計算,本文將模糊數 M 中 a、b、c、d 四個分(fèn)位數的取值局限於(yú)? ?0,1 區間內,具體數值由專家組確定,即上述(shù)每個語義(yì)詞(cí)的四個分位(wèi)數a、b、c、d 都是通過專(zhuān)家組加權平均的方法(fǎ)得到,本文所規定的語義詞所(suǒ)對應梯(tī)形模糊數如表 3.1 所示(shì)。
表 3.1 語義詞對應的梯(tī)形模糊數(shù)
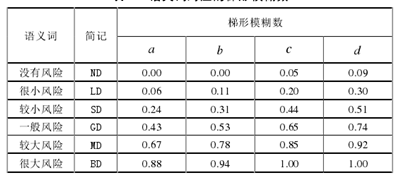
表 3.1 中的各個語義詞模糊數隸屬函數圖像如圖 3.1 所示,圖中的折線代表了(le)相應語義詞的隸屬函數。
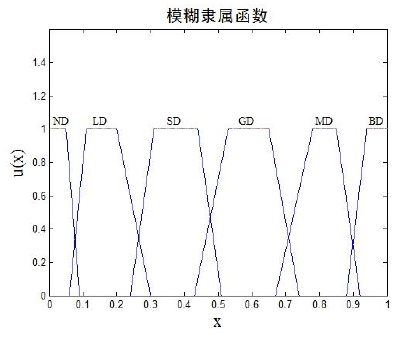
圖 3.1 語義詞對應(yīng)的梯形模糊函數圖像(xiàng)
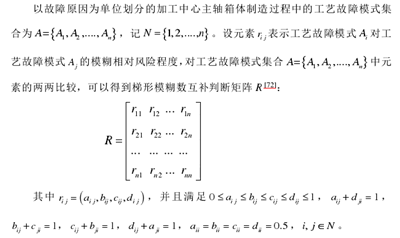
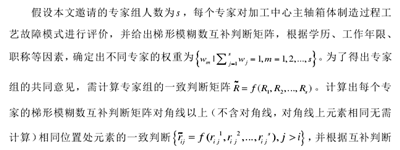
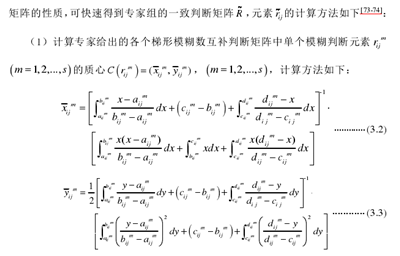
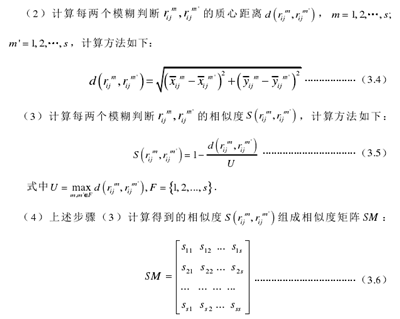

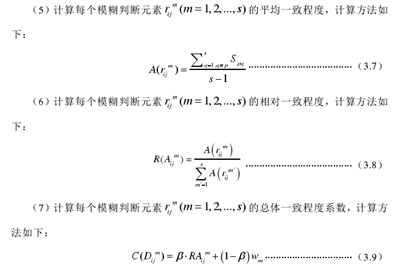
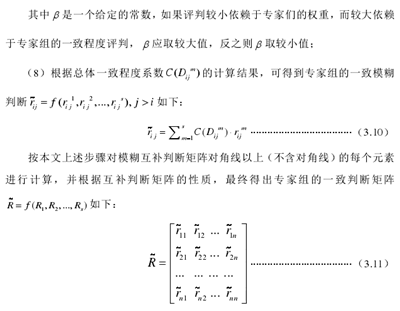

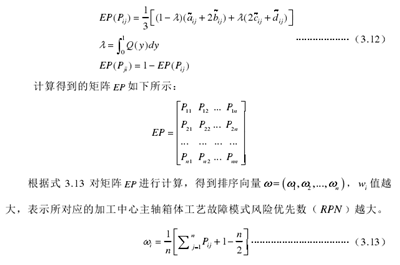
3.2.2 工(gōng)藝係統模糊綜(zōng)合評判方法
對加工中心主軸箱體的整個製(zhì)造工藝係統實施模糊綜合評判,可以為是否對薄(báo)弱工序實施改進措施提供參考,具體方法如下所示[76]:
(1)建立製(zhì)造工藝係統(tǒng)綜(zōng)合評價的評(píng)判等級,等級(jí)V 是對加工中心主軸箱體工藝故障模(mó)式狀態的 h 個評價決斷即 ? ?1 2, ,...,hV ?v v v ;
(2)以上述評判等級為(wéi)標準,專(zhuān)家組對加工中(zhōng)心主軸(zhóu)箱體工藝故障(zhàng)模式集(jí)合? ?1 2= , ,....,nA A A A 中各元素進行評判,並根據各個專家(jiā)的(de)權重得到評判矩陣 PA ,? ?1 2 ,...,i i i ihPA ?? ? ? 表示工藝故障模式iA 的評判集iPA ,集(jí)合中ij? 表(biǎo)示工藝故障
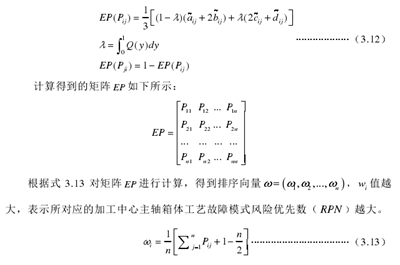
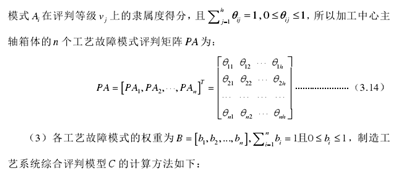
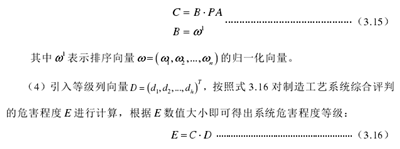
3.2.3 采用模糊評判的工藝 FMECA 分析流程
采用梯形模糊評判方法的加工中心主軸箱體製造工藝 FMECA 的分析流程可概(gài)括為圖 3.2 所示,其主要區別是將工(gōng)藝 FMECA 原有的風(fēng)險(xiǎn)優(yōu)先數( RPN )評分改(gǎi)為梯形模糊評判,相(xiàng)應的工藝 FMECA 表格也會進行修改,各流程的具體內(nèi)容可(kě)參考本章的(de)實例分析。
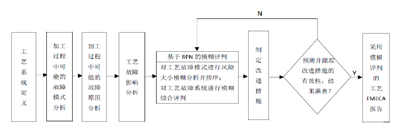
圖 3.2 采用模糊評判的加工(gōng)中心主(zhǔ)軸箱體製造工藝 FMECA 流(liú)程
3.3 實例(lì)分析
本文以某型號加工中心主軸箱體(tǐ)(如圖 3.3 所示)製造工(gōng)藝為例,結合圖(tú) 3.2中的分析流程對其應用基於模(mó)糊評判的製(zhì)造工藝 FMECA 方法,從而能夠在缺少生產過程統計數據的情況下,確定出薄(báo)弱工序並製定相應的改進措施,達到保障加工中(zhōng)心主軸箱體(tǐ)製造工藝可靠性的目(mù)的。為了便於理解和表達,本文以該型(xíng)號加工中心主軸箱體的 2 道工序出現的 4 種故障原因引起的工藝故障模式為例進行分析。
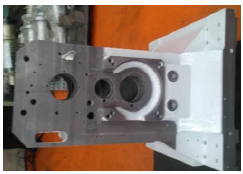
圖 3.3 某型號加工中心主軸箱體
3.3.1 係統定義
加工中心主軸箱體是承載主軸的(de)關鍵零件,其製造精度(dù)對(duì)整機的加工精度有著重要影響;該(gāi)型號主軸箱體(tǐ)毛坯為鑄件,體積(jī)較大並且(qiě)加工精度(dù)要求(qiú)高,加工(gōng)過程中裝夾費時(shí)費力,而且運輸困難,具有較大的(de)加工難度。 3.3.2 “工藝流程表”及“零部件-工藝關係矩陣”的繪製
繪製“工藝流程表”(見表 3.2)及“零部件-工藝關係矩(jǔ)陣”(見表 3.3)。
表 3.2主軸箱(xiāng)體工藝流程(chéng)(部分)
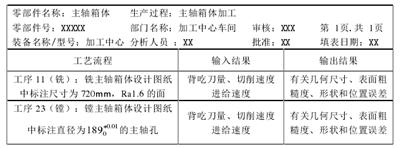
表3.3 零部件-工藝關係矩陣(zhèn)(部分)
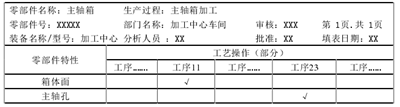
3.3.3 分析(xī)主軸箱體工藝故障模式、原因及影響
對加工中心主軸箱體各工序可能(néng)發生的工藝故障模式、相應的工(gōng)藝故障(zhàng)原因及(jí)影響進行分析,並以故障(zhàng)原因為單位對工藝故障(zhàng)模式編號(見表 3.4)。
表 3.4 主軸箱體工藝故障模式、工藝故障原因及影響(部分)
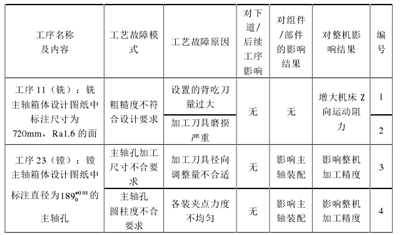
3.3.4 模糊對比(bǐ)評(píng)判計算
以風險優先數( RPN )為模糊評(píng)判原則,本文共(gòng)邀請 5 位加工中心主軸箱體製造領域專家對所編號的工(gōng)藝故障模式進(jìn)行評判,根據(jù)工作(zuò)年限、職稱、學曆等賦予各專家(jiā)的權重如表 3.5 所示。根據互補判斷矩陣的性質,專家組隻需要給出對角線以上的評判元素(sù)即可,具體評分如表(biǎo) 3.6 所示。
表 3.5 專家權重(chóng)分配

表 3.6 專家組模糊對(duì)比評分
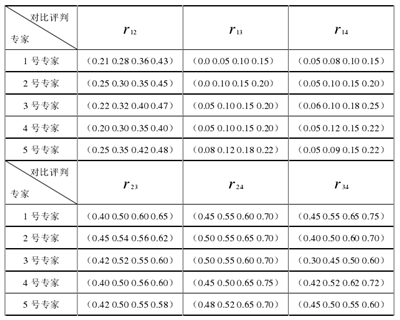
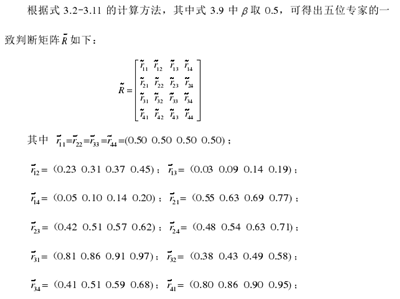
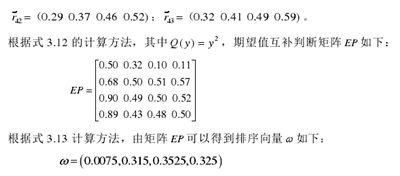
根據? 計算結果可以發現,編號為 3 的加工中心主軸箱體工藝故障(zhàng)模式即由加工刀具徑向調整量不合適引起的主軸孔加工尺寸不合要求,是表 3.4 中所編號(hào)的工藝故障模式中風險最大。 3.3.5 模糊綜合評判計算
對加工中心主軸箱體製造工藝係統(tǒng)實施模(mó)糊綜合評判,建立評判等級V??風險很高,風險較(jiào)高,中等風(fēng)險,輕度風險?,邀請上述 5 位專家對表 3.4 中全部工藝(yì)故障(zhàng)模式進行評判,評分如表 3.7 所。
表 3.7 專家組模糊綜(zōng)合評分
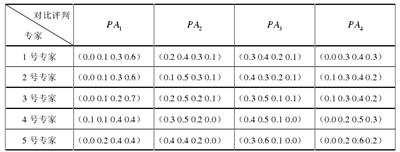
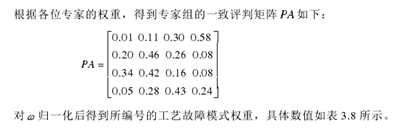
表 3.8 編號的各工藝(yì)故障模式權重分配

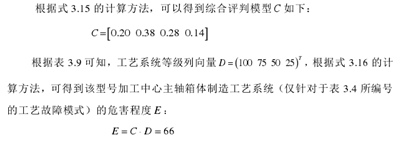
由表 3.9 可知,該(gāi)型號加工中心主(zhǔ)軸箱體製造工藝係統(僅針對表 3.4 所編號的工藝故障模式)風險較高,因此有必(bì)要(yào)針對薄弱工序采取改進措施,減少工藝故障的發生,比如對工(gōng)序 23 建立關鍵工序質量控製點(diǎn)。
表 3.9 係統評判等級與改進措施
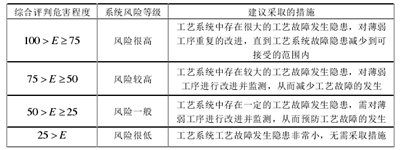
3.3.6 基於模糊評(píng)判的(de)工藝 FMECA 表格
根據模糊評(píng)判的結(jié)果,針對不同工藝故障原因引起的加工中心主軸(zhóu)箱體製造工藝故障模式采取改進措施,直到(dào)發生的工藝故障模式風險程(chéng)度降低到符合規定要求為止(zhǐ)。例如針對工序 23 中的(de)工藝故障模式“主軸孔加工尺寸不合要求”采取了(le)“合理調整加工刀具徑向調整量,調整完之後進行檢查,對該工序建立關鍵質(zhì)量控製點(diǎn)”的改進措施,對(duì)改進措施進行跟蹤後,專家組對(duì)其風險評價為“風險很(hěn)小”,驗證了改進措施的有效性。將上述工作內容進行整理,製定采用模糊 評判方法的加工中心主軸箱體製造工藝 FMECA 表格(gé)(如表 3.10 所示(shì),見下(xià)一 頁)。
表 3.10 采用模(mó)糊評判的加工中心主軸箱體工藝(yì) FMECA 表(部分)
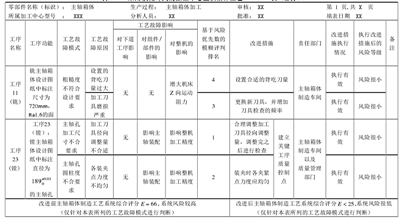
3.4 本章小結
本章介紹了加工中心主軸箱體製(zhì)造工藝 FMECA 實施流程,以風險優先(xiān)數為判原則對以故(gù)障(zhàng)原因為單(dān)位的工藝故障(zhàng)模式(shì)應用梯形模糊數評判方(fāng)法,通過對其風險程度的兩兩比較並對專家組評分進行計算,從而得(dé)出各工藝故障模式的風險程度排序,對加工中心主軸(zhóu)箱體整個製(zhì)造工藝係統進行綜合評判,確(què)定出係統風險等級,為是否實施改進措施提供(gòng)依據。本章以某型號加工中心主軸箱體的製(zhì)造工藝為例,對其應(yīng)用了基於模糊評判的製造工藝 FMECA 方(fāng)法,得出各工藝故障模式(shì)風險排序(xù)以及整個製造(zào)工藝係統的風險評判等級,製(zhì)定了針對(duì)各個(gè)工藝故障模式的改進措施,並對改進措(cuò)施的有效性進行了驗證,從而降低了整個工藝係統的風險等級,達到(dào)了保障加工(gōng)中(zhōng)心主(zhǔ)軸箱(xiāng)體(tǐ)製造工(gōng)藝可(kě)靠性的目的,也驗證了基於模糊評判的加工中心主(zhǔ)軸箱體(tǐ)製造工藝 FMECA 方法的可行性(xìng)。
第 4 章加工中心主軸箱體製造過程控製圖分析及軟件編製
工藝 FMECA 方法能夠針對發(fā)生的工藝故(gù)障采(cǎi)取相應改進(jìn)措施,實現對加工中心主軸箱體製造工藝可靠性(xìng)進行保障的目的,具有直接有效的特點,但工藝FMECA 方法並不能在工藝故障(zhàng)發生之前(qián)及時發現生產過程中存(cún)在異常因素,所以無法對工藝故障的發生起到預防作用,因此本章將研究以預防工藝故障(zhàng)發生為目的的控製圖分析方法,從而彌(mí)補工藝 FMECA 方法所存在的不足。 控製圖分析方法又被稱作統計(jì)過(guò)程控製(SPC),可(kě)以在工序質量(liàng)特性值(zhí)符合規定要求的情況(kuàng)下判斷出加工中心(xīn)主軸箱體製造過程是否存在異常因素。若不存在異常因素,可以通過控製圖對加工中心主軸箱體(tǐ)製(zhì)造過程進行監控,從而(ér)保障加工中心主軸箱(xiāng)體製造過程處於穩定狀態(tài);若存在異常因素(sù),通過對異常因素的排(pái)查(chá)能夠預防或者減少工藝故(gù)障的發生,使生產過程處於穩(wěn)定狀(zhuàng)態,從而提高加工中心主軸箱體製造工藝穩定性。判斷工序質量特性值(zhí)分(fèn)布異常(cháng)的條件較多(duō),為了能夠降低操作人員工作強度,並能(néng)快速準確的判別加工過程是否處於(yú)穩定狀(zhuàng)態,本章采用 MATLAB 的(de) GUI(圖形用戶界麵)編製(zhì)了加工中心主軸箱體製造過程控製圖分析軟件(jiàn)。
4.1 加工中心主軸(zhóu)箱體製造過程控製圖分析
4.1.1 控製圖分析原理
控製圖分析方法[77]是美國 W. A. Shewhart(休哈(hā)特)以預防工藝故障發生為原則首創的控製過程工具,也被稱為統計過程控製(Statistical Process Control, 簡稱 SPC)。W. A. Shewhart 認為產品的質量特性值在生產過程中存在著波動,引起波動的原(yuán)因有兩種:一種是生產過程中固有的偶然因(yīn)素所造成的偶然波動,另一種是非生產過程中固有的異(yì)常因素(也稱係統因素)所造成的異常波動。偶然因素一直存(cún)在於生產過程中並且無法(fǎ)避免,但是對產品質量影響(xiǎng)較(jiào)小;而異(yì)常因素是時斷時續的存在於生產過程中並且對產品質量影響較大,但可以避免。因此在(zài)生產過程中(zhōng)應利用(yòng)控製圖分析方法準確(què)判(pàn)斷出係統因素所造成的波動是否存在,如果存在異常波動應盡快(kuài)尋找並排除引起異常波動的係統因素,從而能夠預防或者減少工藝故(gù)障的發生,保證(zhèng)生產過程的穩定。
文27
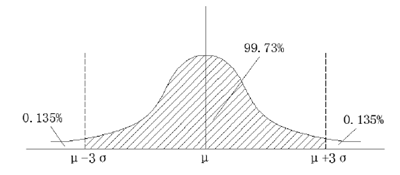
圖 4.1 正態分布曲線(xiàn)

圖 4.2 工序樣本質量特性(xìng)值描點圖(tú)
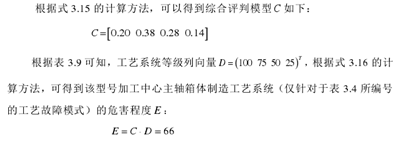
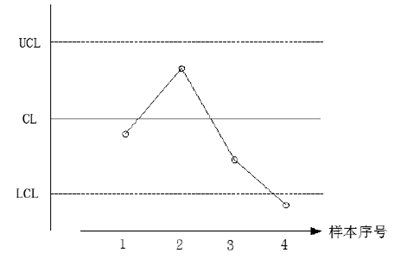
圖4.3 控製圖(tú)形式
控製圖可以分為分析用控製圖和(hé)控製用控製圖,分析用控製圖是用於(yú)判別生產過程中是否存(cún)在異常情況以及工序能(néng)力指數是(shì)否符合要求,控(kòng)製用控製圖是以當前(qián)穩定的生產狀態衡量後續生產的工件質量特性值是否穩定(dìng)。控製圖又可以分為計量(liàng)值控製圖、計點值控製圖以(yǐ)及計件值控製圖。計量值中應用較多的是均值
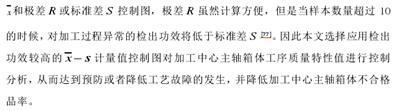
4.1.2 加工中心主軸箱體製造工序控製圖分析流程
目前控製圖分析方法(fǎ)已經形成(chéng)相應的國家標準以及國際標準[78-80],根(gēn)據標準的要求,加工中心主軸箱體製造工序控(kòng)製圖分(fèn)析(xī)流(liú)程如下: (1)準備工作:確定所要分析加工中心主軸箱體製造工序的質量特性值 X,根據生產情況按一定(dìng)的時(shí)間間隔采集樣本,並根據時(shí)間順序進行分組和排序,樣本容量 n 為 4 ~ 5個,並保證樣本容量相同,樣本個(gè)數 K 為 20 ~ 30 個,記錄采集到的樣本數據。
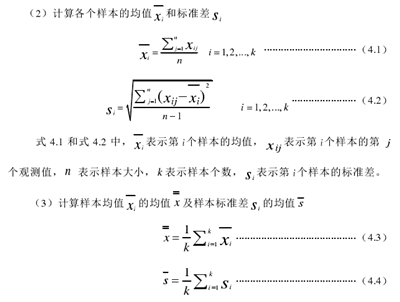

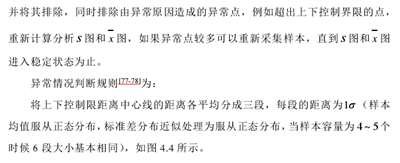
1)有 1 個點落(luò)在區域 A 之外;
2) 連(lián)續 3 個點(diǎn)有 2 個點落在 A 區;
3) 連續 6 個及以上的點出現(xiàn)遞增或(huò)者遞減趨勢;
4)連續 9 個(gè)及以上(shàng)的點出現在(zài)中心線同一側;
5) 連續 5 點中有 4 點落在中心(xīn)線一(yī)側的 C 區(qū)之外;
6) 連續 8 點落在中心線兩側並且未(wèi)落在 C 區內;
7) 連續 14 個點中相鄰點交替上下;
8) 連續 15 點落在中心線(xiàn)兩側的 C 區內;
9)點子呈現周期性變化。
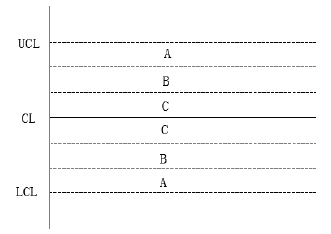
圖 4.4 控製圖區域劃分
(6)判斷該加工中心主軸箱體製造工序質量特性值及控(kòng)製圖(tú)修正後的工序能力指數是否符合規定要求,對其它要求的(de)判斷可(kě)根據實際生產情況進行。如(rú)果有生產要求不符合規定的(de)情況,應對相關生產因素進行調(diào)整,最終將分析用控製圖的控製界限延長從而轉為控製用控製圖。
(7)作控製(zhì)用控製圖對加工中心主軸箱體生產過程進行控製,按流程(1) 中確(què)定的采集樣本方法采集後續生產的樣本數據,並在控製用控製圖中描點, 判(pàn)斷是否存在異常。
(8)一段時間後應根據實際質量水平對控製用控製圖的中心(xīn)線和控製界(jiè)限進行修(xiū)正。
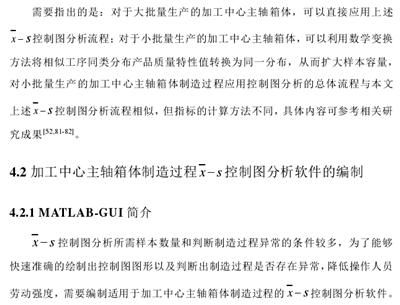
該軟件應具備數據錄入、數據計算、圖形繪製以及製造過程異(yì)常判斷等功能,同(tóng)時(shí)能夠記錄(lù)加工中(zhōng)心主軸箱(xiāng)體製造過程(chéng)發生的工藝故障模式(shì)、工藝故障原因及影響等,為技術人員提供統計數據,當記錄的數據足夠豐富時可以直接應用於工藝FMECA 分析中而(ér)不需要采取模糊評判等數學(xué)方法,從而簡化分析過(guò)程。 目前編程語言種類豐富如 Java、C、C++、Visual Basic、MATLAB 等,且具備各自獨特的優點,因此根據不同的編程(chéng)要求及應用領域選擇合適的語言可以提高編程效率並獲得運行穩(wěn)定的程序。MATLAB 是一種廣泛用於數據分析、數值(zhí)計算、數據可視化、建模仿真、算法開發等多個方麵的高級計算語言和交互環境,並且提供了大量現成(chéng)的函數(shù),具有(yǒu)計算效率高、編(biān)程(chéng)效率高、操作方便等優點(diǎn)[83]。因此本文采用 MATLAB-GUI(圖(tú)形用戶界麵)編製加工(gōng)中心主軸箱體製造過(guò)程x ?s 控製圖分析(xī)軟件。 MATLAB-GUI 指的是 MATLAB 圖(tú)形用戶界麵(miàn)(Graphical User Interfaces,GUI)設計。本(běn)文以 MATLAB7.10 版本為例介紹 GUI 設計窗口,如圖 4.5 所示。GUI 設計窗口的上方為菜單欄,包括“File”、“Edit”等6個菜單項;菜單欄下方為工具(jù)欄,用於打(dǎ)開布局編(biān)輯器、打開菜單編輯器等;網格區的左側為控件工具箱,包括按(àn)鈕、可編輯文本框等控件對象;網格區為設計區,用於布置(zhì)菜單和控件對象。
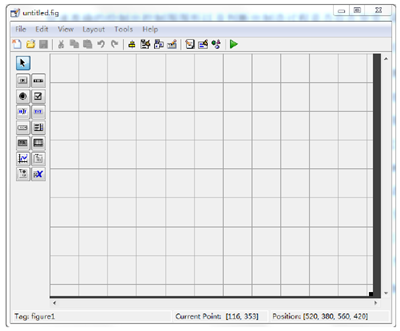
圖 4.5 MATLAB 7.10 版本的 GUI 設計窗(chuāng)口
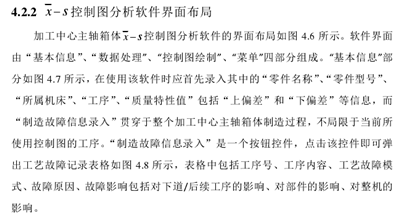
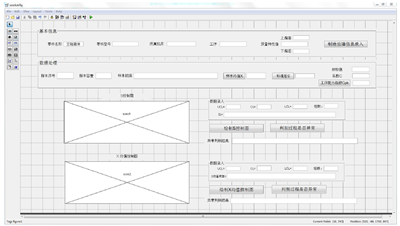
圖 4.6 加工中心主軸箱體 x?s控製圖分析軟件的界(jiè)麵布(bù)局
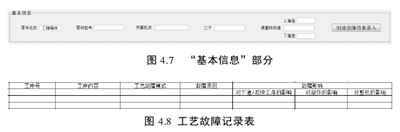
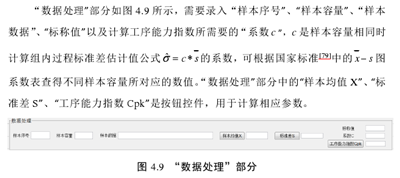
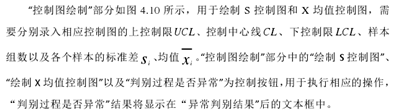
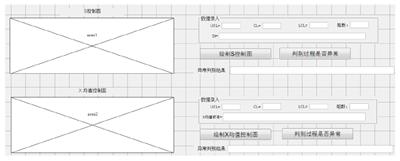
圖 4.10 “控製圖”繪製部分
“菜(cài)單(dān)”部分如圖 4.11 所(suǒ)示,包括“保(bǎo)存”、“退(tuì)出”、“軟件說(shuō)明(míng)”三個功能,“保存(cún)”功能是將整(zhěng)個軟件界麵以圖片形式進行保存(cún),“軟件說明”是點擊之後彈出 word 文檔如圖 4.12 所示,用於說明或者解釋軟件(jiàn)的一些(xiē)信息,對於4.1.2 節中異常判斷原則中的(de)點子呈現周期性變化,需要通過對控製(zhì)圖形狀觀察可得。
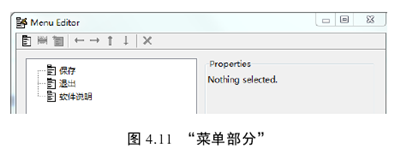
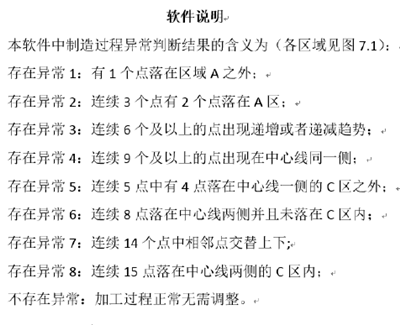
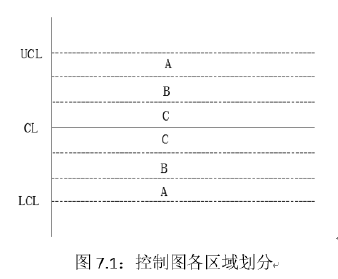
圖 4.12 軟件說明
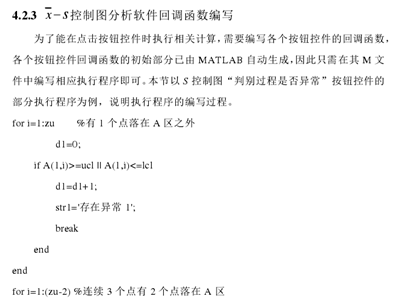
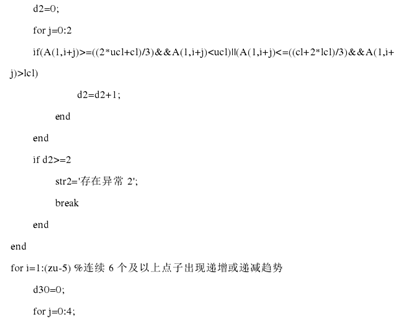
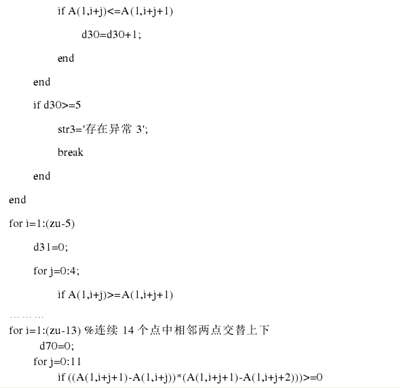
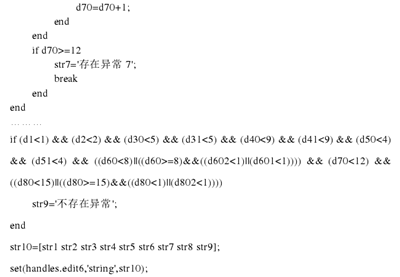
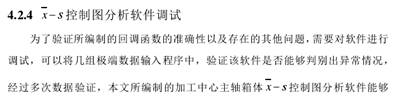
滿足所要(yào)求的功能,並且參數計算及異常結果的判斷均準確無誤,由(yóu)於下(xià)一節將進行實例分析,因此本節對(duì)軟件調試驗證的具體過程不進行詳細描述。 4.3 實例(lì)分析
4.3.1 數據采集與(yǔ)處理
根據 4.1.2 節中的(de)要求,采集了(le)某型號加工中心主軸箱(xiāng)體(tǐ)製造工序 23 的樣本,樣本數量(liàng)為 25 組,樣本容量為(wéi) 4,並對樣本數(shù)據進行了計算處理,具(jù)體數據如(rú)表 4.1 所示。
表 4.1 數(shù)據記(jì)錄(lù)表
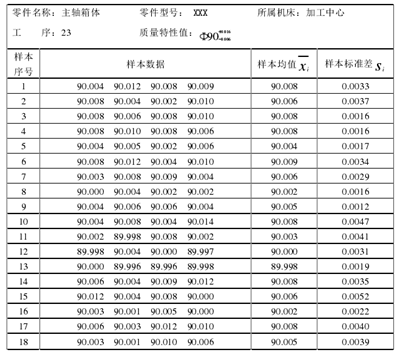
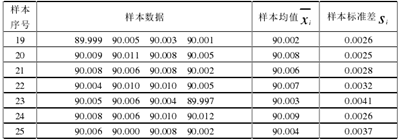
4.3.2 控製圖參數計算
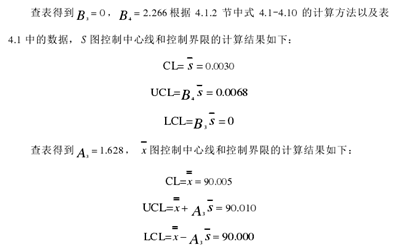
4.3.3 作分析用(yòng)控製圖及控製用控製圖

件的判別結果可以發(fā)現第(dì) 12 個樣本和第 13 個樣本均值超出控製界限,因此需要查找造成點子出界的異常原因,通過調查發現是工人(rén)師(shī)傅未能按規(guī)定要求及時調整加工刀具(jù)的調(diào)刀(dāo)量,因此需要讓操作工人嚴(yán)格遵守生產規定進行操作。 將異常點即樣本(běn) 12 和樣本 13 的均值和標準(zhǔn)差排除,對剩(shèng)餘的 23 個樣本重新繪製控(kòng)製圖,並按照式 4.1-4.10 計算新的控製界(jiè)限(xiàn),如圖 4.14 所示,可以發現 S
圖(tú)和 x 圖均無異常,且樣本數據均符合生產要求,工序能力指數 Cpk為 1.02,表明工序能(néng)力(lì)尚可,因此可以將去除異常點後的控製圖作(zuò)為控製(zhì)用控製圖,對後續生產進行控製,並經過一定時間(jiān)後對控(kòng)製界限進行(háng)調整。

圖 4.13 繪製的分析用控製(zhì)圖
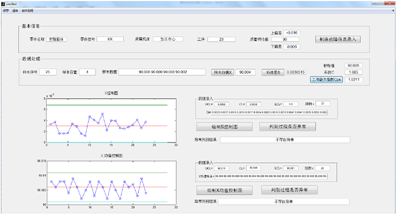
圖(tú) 4.14 去除異常點後的控製圖
4.4 本章小結
本章(zhāng)介紹了控製圖(tú)分析(xī)方法的原理以及加工中心主軸箱體製造(zào)過程控(kòng)製圖分析步驟,利用 MATLAB-GUI(圖形(xíng)用戶界麵)編製了加工中(zhōng)心主軸箱體製造過程 x ?s 控製(zhì)圖分(fèn)析軟件,該軟(ruǎn)件具備數據錄入、數據計算處(chù)理(lǐ)、繪(huì)製控製圖、判(pàn)斷製造(zào)過程是(shì)否異常、記錄工藝故障數據等功能,通過實例分析表明所編(biān)製軟(ruǎn)件能夠準確快速計算樣本數據、繪製分(fèn)析用 S 圖和 x 圖、判斷出(chū)加工中(zhōng)心主軸箱體製造過(guò)程是否存在異常,通過對異常因素和異常樣本數據的排除(chú)可以生成相應的控(kòng)製用控製圖,用於監測後續加工中心主軸箱體製造過程的波動情況。因此本章所研究的控製圖分析(xī)方法能夠保障加工中心主軸箱體(tǐ)製造過程(chéng)的穩(wěn)定,預防製造工藝故障的發生,從而達到保障(zhàng)加工中心(xīn)主軸箱體製造工藝可靠性的目的。
投稿箱:
如果您有機床行(háng)業、企業相(xiàng)關新聞(wén)稿件發表,或進行資訊合作,歡迎聯係本網編輯部, 郵箱:skjcsc@vip.sina.com
如果您有機床行(háng)業、企業相(xiàng)關新聞(wén)稿件發表,或進行資訊合作,歡迎聯係本網編輯部, 郵箱:skjcsc@vip.sina.com
更(gèng)多本專題新聞
專(zhuān)題點(diǎn)擊前十
| 更多